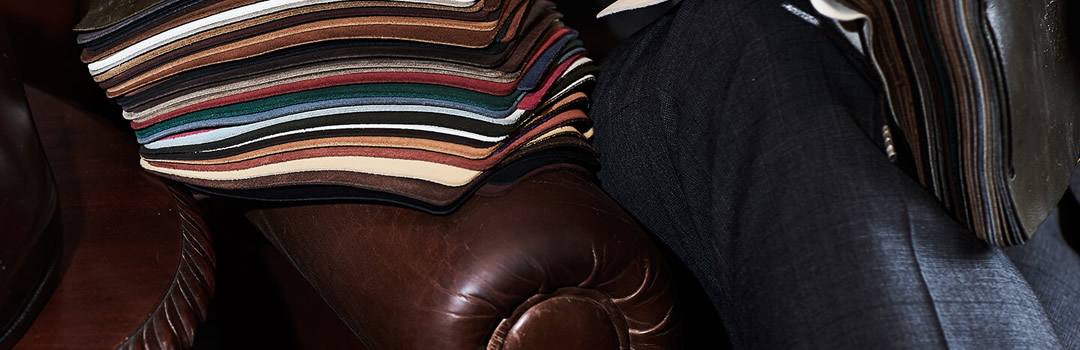
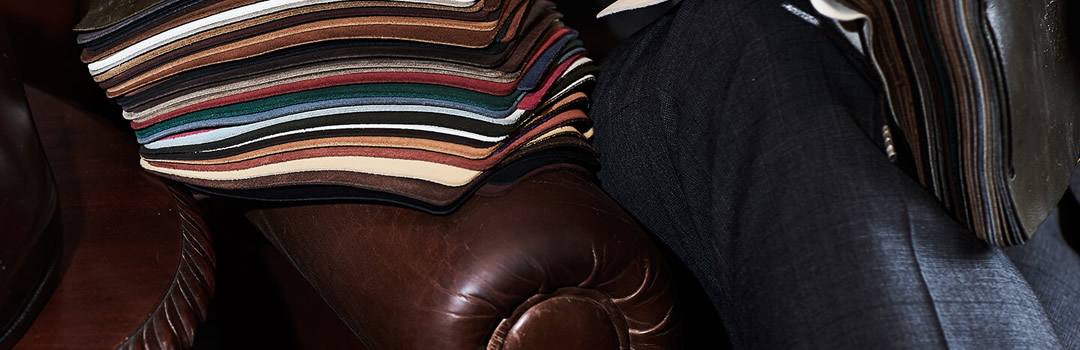
Leather knowledge
Leather knowledge
Leather factory production process
When it comes to leather, everyone is the most familiar. Most people pay more attention to leather, shape, function, size, color, etc. When it comes to the production process, few people know about it. Today, let’s reveal the secret of leather production. The process flow in, is generally divided into the following steps, but there will be some differences between the types and uses of the leather.
01. Pickled raw hides
The skin that has just been peeled off is called fur or raw hide. It cannot be used as shoes. In order to reduce the moisture of fresh raw hides, inhibit the growth and reproduction of bacteria, and slow down the hydrolysis of enzymes for storage and transportation, the raw hides that have just been peeled are generally salted first. Wet salted leather can be stored for 3 to 5 months. If it needs to be stored for a longer period of time, the wet salted leather must be dried into dry salted leather.
02. Remove dirt
Then the salted raw hides with fur are soaked in a large container filled with salt water. The purpose is to remove the dirt, impurities and excess oil on the surface of the raw hides, and then rinse with clean water.
03. Fur separation
After completing the above two steps, we need to separate the skin and hair to remove the hidden meat and grease in the skin. The traditional meat extraction process is to place the raw skins on a semi-cylindrical platform to manually scrape the meat. Afterwards, the raw skin with fur is immersed in a calcium-sulfur mixture, and the fur and the skin are quickly separated. Salt and acid are additionally introduced in the decalcification and pickling stages to prepare for the subsequent tanning. However, for efficiency, lime is now used for hair removal and to decompose unnecessary grease and collagen fibers.
04. Fermentation
Fermentation is also called softening. Add fermentatives and emulsifying degreasing agents to the pool that separates fur and skin (deliming) to remove tissue collagen and non-collagen proteins, increase the softness and elasticity of the cortex, and also improve skin loss. The effect of ash improves the cleanliness and smoothness of the leather surface. After these processes are completed, we call it blue leather or wet blue leather.
05. Tanning (generally divided into vegetable blend and chrome blend)
Put the wet blue leather in a tannin trough (a container for tanning leather). Traditionally, vegetable tannins (also known as plant polyphenols) extracted from plants are used as the main ingredient of the tanning agent, and the vegetable tanning agent is added Soaking and tanning the leather in a tannin tank is an important step that consumes a lot of time and energy.
06. Dehydration
The leather soaked in the tannin tank is washed repeatedly and then dehydrated.
07. Leather layering
At this time, the leather is thicker and uneven. It needs a machine to separate the leather into several layers. The first layer is the best leather surface, usually used for high-end leather shoes and bags; the second layer is malleable leather for imitation deer Leather and other products.
08. Oiling
The purpose is to maintain its softness and change the color of the leather itself. Usually the oil used in tanning is golden fat like honey.
09. Dry
After the leather has fully absorbed the grease, it will use a drying oven or a vacuum oven to dry the leather and hang it until it is dry. After these are completed, we usually call it crust.
10. Ironing
After drying, the leather will be uneven, usually by machine ironing or leather rolling to restore the softness of the leather.
11. Subsequent processing
If you want to achieve the desired effect and color of the finished leather embryo, you need to finish the leather. In the finishing stage, polishing, coloring, sanding, sanding, embossing, etc. can be realized. Later, protective measures will be taken to prevent some chemical products and weather from harming the leather, and the color of the leather will be more uniform through multiple dyeing.
